A Quality Management Plan (QMP) is a formal document that outlines how an organization will ensure the quality of its products, services, or processes. It defines quality objectives, assigns roles and responsibilities, describes quality control methods, and establishes metrics for assessing performance. The plan also includes procedures for reviews and audits, with a focus on continuous improvement. Its main goal is to meet or exceed customer expectations and regulatory standards.
Building A Quality Management Plan
In today’s highly competitive business environment, the importance of quality management and lean operations cannot be overstated. Implementing a robust Quality Management System (QMS) and a lean manufacturing approach can significantly enhance a company’s efficiency, reduce waste, and ensure that products meet or exceed customer expectations. This blog will delve into the development and implementation of a quality management and lean operations program, exploring essential elements such as control procedures, standard operating procedures (SOPs), ISO 9000 standards, and various quality management tools and techniques. We will also examine the impact of quality pioneers like W. Edwards Deming, Joseph Juran, and Philip B. Crosby on modern quality practices. Join us as we explore how these strategies can transform your manufacturing processes and drive your organization towards excellence.
Quality management is a systematic approach to producing merchandise or services that meet or exceed customer expectations. By employing a Quality Management System (QMS), organizations create a constancy of purpose toward product improvement, enhance the production process, reduce expenses, and achieve consistent product quality (Russell & Taylor, 2023). Building a quality management plan involves the implementation of control procedures, standard operating procedures (SOPs), ISO 9000 standards, and various tools developed for quality management and continuous improvement. This approach positions operations managers to effectively deploy their resources.
An effective QMS includes detailed control procedures. Implementing checkpoints at various stages of production provides valuable insights into the operation, ensuring that each step meets quality standards before proceeding. This systematic monitoring helps identify and address issues promptly, maintaining high-quality output throughout the production process. To ensure consistent quality, operations managers develop a set of SOPs. These procedures enforce a standard conduct across the organization, ensuring that all employees follow the same protocols. Training workers to these standards is critical; the closer the workers adhere to the SOPs, the more productive and efficient the operation becomes. This consistency not only improves product quality but also enhances operational efficiency, leading to better overall performance.
A global initiative to drive baseline standards in quality management has been demonstrated through the International Organization for Standardization (ISO). Russell and Taylor (2023) discuss the ISO 9000 series, which addresses quality management by applying uniform expectations across various industries to adhere to a certain level of quality and consistency. These standards ensure that organizations maintain a baseline of quality, fostering trust and reliability in their products and services. While the ISO 9000 outlines broad standards, individual companies should develop their own specific procedures tailored to their unique operational needs and market goals. This approach not only ensures compliance with industry standards but also provides the organization with a distinct competitive advantage. By differentiating their products and services, companies can enhance the customer experience through greater selection and innovation, ultimately driving profitability and competitive eligibility.
QMS employs various tools and techniques aimed at ensuring product quality and continuous improvement. One such tool is Statistical Process Control (SPC), which uses statistical methods to monitor and control production processes. SPC helps identify variations that could lead to defects and provides opportunities for timely adjustments to maintain quality standards (Russell & Taylor, 2023). Another key technique is Six Sigma, which seeks to reduce process variation and improve processes. Six Sigma employs the structured DMAIC methodology (Define, Measure, Analyze, Improve, Control) to systematically eliminate defects and enhance overall quality (Russell & Taylor, 2023). These tools and techniques collectively contribute to the effectiveness of a QMS by fostering a proactive approach to quality management and continuous improvement. Total Quality Management (TQM) is another approach that QMS leverages for continuous improvement and customer satisfaction. TQM involves all levels of the organization, fostering a culture of quality and collective responsibility. The Plan-Do-Check-Act (PDCA) cycle is a systematic format for problem-solving within TQM, which helps organizations continuously improve their processes by planning, executing, checking the results, and acting on those findings (Russell & Taylor, 2023). Providing comprehensive training programs for all employees on the use of SPC, Six Sigma, and TQM is crucial for effectively applying these frameworks in operations. Training ensures that employees understand and can implement these quality management tools and techniques, which is essential for the successful execution of the quality management plan. Additionally, establishing key performance indicators (KPIs) enables the company to monitor the effectiveness of these programs. Regularly reviewing performance data and making necessary adjustments supports the organization’s efforts to achieve the highest level of success and maintain continuous improvement in quality management.
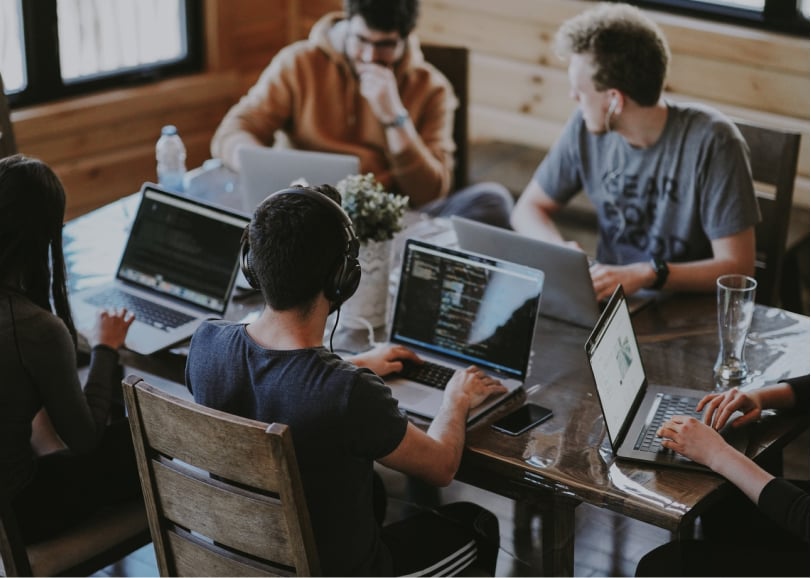
Lean Implementation Plan
Implementing a lean system in a manufacturing company involves adopting principles and practices aimed at maximizing value while minimizing waste. Lean manufacturing aims to create more value for customers with fewer resources by optimizing workflows and eliminating non-value-added activities. According to Russell and Taylor (2024), the primary goal of lean implementation is to enhance efficiency and streamline production processes. By focusing on continuous improvement and involving all employees in the process, lean systems foster a culture of efficiency and quality.
Implementing a lean system requires a structured approach to optimize workflows and eliminate inefficiencies. One of the first steps in this process is Value Stream Mapping (VSM). VSM involves mapping out all the steps in the production process to identify areas where waste occurs and opportunities for improvement exist (Russell & Taylor, 2024). By visualizing the entire production flow, organizations can pinpoint non-value-added activities and make targeted changes to enhance efficiency. The 5S Methodology is another critical component of lean implementation. This method focuses on creating a clean, organized, and efficient workspace by following five principles: Sort, Set in order, Shine, Standardize, and Sustain (Russell & Taylor, 2024). Implementing the 5S principles helps to improve workplace safety, reduce waste, and increase productivity.
Kaizen, or continuous improvement, is a fundamental philosophy in lean systems. It encourages all employees to contribute to ongoing improvements in the production process. Kaizen involves regularly reviewing processes, identifying inefficiencies, and making incremental changes to enhance productivity and quality (Russell & Taylor, 2024). By fostering a culture of continuous improvement, organizations can adapt more quickly to changes and continuously enhance their operations. Effective strategies for waste reduction are essential in lean systems. This involves identifying and eliminating the seven types of waste: overproduction, waiting, transportation, overprocessing, excess inventory, unnecessary motion, and defects (Russell & Taylor, 2024). Streamlining production processes by focusing on these waste areas can significantly improve efficiency and reduce costs.
To further enhance efficiency in a lean system, several tools can be utilized. Just-in-Time (JIT) is a production strategy that aims to reduce inventory costs by receiving goods only as they are needed in the production process, thereby minimizing waste. JIT ensures that materials and products are delivered exactly when they are required, reducing storage costs and improving cash flow (Russell & Taylor, 2024). Kanban is another essential tool in lean manufacturing that helps manage workflow and inventory. It uses cards to indicate when new materials are needed in the production process. This system helps prevent overproduction and ensures that inventory levels are kept at optimal levels. Cellular Manufacturing is a method that groups different types of machinery and equipment into a cell that can produce a family of products. This setup minimizes movement and handling, reduces lead times, and enhances production efficiency (Russell & Taylor, 2024).
Monitoring and measuring performance are critical components of a successful lean implementation. Establishing key performance indicators (KPIs) allows organizations to track the effectiveness of their lean initiatives. KPIs should be specific, measurable, achievable, relevant, and time-bound, providing clear metrics for evaluating performance. Regular review and adjustment of processes based on KPI data are essential to ensure continuous improvement. By consistently monitoring performance and making necessary adjustments, organizations can sustain the benefits of lean systems and continuously enhance their operations. Implementing these tools and strategies as part of a comprehensive lean system enables manufacturing companies to improve efficiency, reduce waste, and maintain high-quality standards, ultimately delivering greater value to customers.
Impact of Quality Pioneers
Quality pioneers have played a pivotal role in shaping the principles and practices of modern quality management. Their contributions have significantly influenced how organizations approach quality, ensuring that products and services meet customer expectations and continuously improve over time. Understanding the impact of these pioneers provides valuable insights into the evolution and implementation of quality management systems. W. Edwards Deming is renowned for his contributions to quality management, particularly his development of the Plan-Do-Check-Act (PDCA) cycle. Deming emphasized the importance of statistical methods in quality control and advocated for continuous improvement through systematic problem-solving. His 14 Points for Management highlighted the need for a transformative approach to management, focusing on long-term planning, education, and fostering a culture of quality within organizations. Deming’s principles have had a lasting impact on modern quality practices, particularly in the adoption of Total Quality Management (TQM) and Six Sigma methodologies (Russell & Taylor, 2023).
Joseph Juran introduced several key concepts and methodologies that have become foundational in quality management. His Juran Trilogy—Quality Planning, Quality Control, and Quality Improvement—provides a comprehensive framework for managing quality across all organizational levels. Juran emphasized the importance of top management involvement in quality initiatives and the need for setting clear quality goals. His focus on the customer and the idea that quality should be built into the process, rather than inspected in, have influenced countless organizations in their pursuit of excellence. Juran’s teachings have been instrumental in shaping quality management practices globally (Russell & Taylor, 2023).
Philip B. Crosby is best known for his philosophy that “quality is free” and his principle of “Zero Defects.” Crosby argued that the costs of poor quality far outweigh the investments needed to achieve high quality. He introduced the concept of “conformance to requirements,” which defines quality as meeting the customer’s specifications. Crosby’s Four Absolutes of Quality Management and his 14 Steps to Quality Improvement have provided organizations with practical guidelines for implementing effective quality management programs. His legacy lies in the widespread adoption of his principles, which have helped organizations realize that investing in quality leads to significant cost savings and improved customer satisfaction (Russell & Taylor, 2023). These quality pioneers have laid the groundwork for modern quality management practices, and their contributions continue to influence how organizations approach quality today. By integrating their principles and methodologies, companies can enhance their processes, achieve higher levels of customer satisfaction, and maintain a competitive edge in the market.